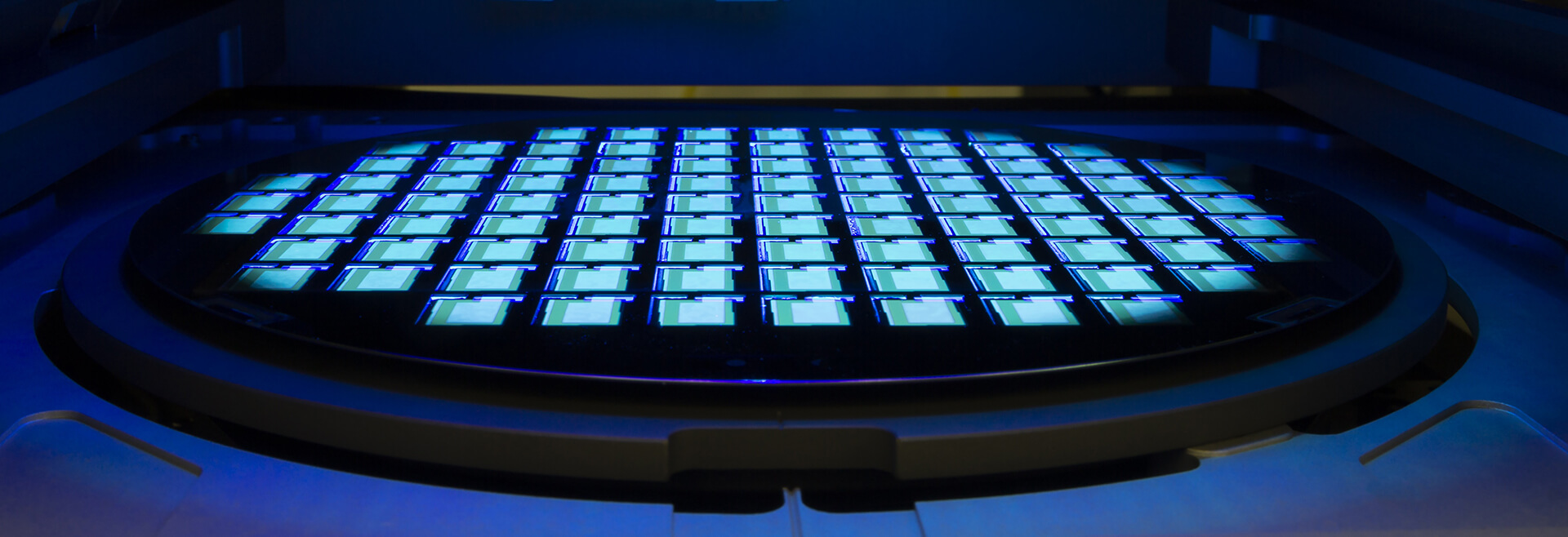
Furnace Systems—Ultra FN Atmospheric Pressure Oxidation/Anneal

High-temperature and high-speed well drive-in for power semiconductors
Emerging power semiconductor applications require the use of silicon-based power devices, which often require processing at elevated temperatures. High-temperature atmospheric pressure annealing and oxygenation allow you to optimize the post-ion implant annealing process with high-temperature and high-speed well drive-in to support power semiconductor manufacturing.
Our Ultra Fn atmospheric pressure oxidation/anneal furnace is designed to address this market’s unique requirements and features a silicon carbide (SiC) chamber and injector in combination with our patented slip-on plate to enable high-speed annealing at 1300°C. Our slip-on plate design is a key differentiator as it prevents wafer slippage and warpage, even at extremely high temperatures. The system is also designed to maximize wafer throughput, using high temperatures to accelerate anneal process times combined with our fast-cooling unit.
Major Benefits
Consistent and Stable Heat Control
The heater is the most critical component in a furnace. To address these demands, the Ultra Fn atmospheric pressure oxidation/anneal furnace heater features a proprietary control algorithm, which provides stable control of temperature, pressure and gas flow rate.
Durability and Reliability
The Ultra Fn atmospheric pressure oxidation/anneal furnace’s innovative design combines ACM’s proven software technology with new hardware to improve the system’s durability and reliability. Using SiC chamber parts increases part lifetime to reduce cost of ownership.
Features & Specifications
- Process temperature up to 1300°C
- Batch processing of 75-100 wafers
- 300mm wafer compatibility
- Quick ramping control heater keeps the temperature within two limits from the bottom to the top of the heating unit, allowing for precise, consistent temperature control across the entire heating chamber
- Fast-cooling unit shortens process time and increases WPH
- Four loadports – two automated, two manual
- FOUP transfer robot and stocker
- Wafer transfer robot
- Loading area O2 control
- IGS gas supply system
- In situ gas cleaning system
- Absolutely pressure control
- SEMI standard
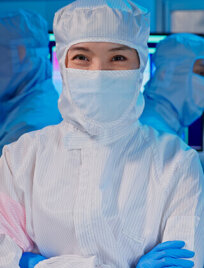
Contact Us
Looking for customized solutions for your wet wafer processing, ECP, Furnace, Track and SFP?