Megasonic cleaning with ACM’s advanced SAPS wafer cleaning technology provides an efficient, resource-optimized solution for the complex challenges associated with photoresist (PR) removal and metal lift-off (MLO) processes in semiconductor manufacturing. In this blog, we explain how the combination of ACM’s Smart Megasonix systems, MegPie transducer, and the active puddle method delivers superior removal performance with good uniformity and particle neutrality. Learn how implementing ACM’s approach successfully cuts traditional PR and MLO process times from several hours at high temperatures to minutes at lower temperatures.
Megasonic cleaning can be deployed for several process applications, including photoresist (PR) removal and metal lift-off (MLO). If you’re seeking an alternative to photolithography and etch processes, this technique eliminates an etch process step, reducing cost, optimizing cycle times and sharply reducing chemical demand at high temperatures.
Historically, the MLO process has posed challenges including metal retention, formation of sidewall “ears,” or redeposition of metal particles. Additionally, MLO, photoresist develop and strip, and polymer removal from high-aspect-ratio features such as through-silicon vias (TSVs) are dependent on chemical reaction kinetics. Even with aggressive chemistries, the traditional cycle times are on the order of several hours at temperatures as high as 90°C for legacy industry processes of record (PORs).
Enhanced megasonic cleaning with SAPS
Megasonic cleaning as applied in semiconductor device manufacturing strongly relies on the phenomenon of acoustic cavitation – the formation and collapse of bubbles in liquid irradiated by intense ultrasound. Because acoustic cavitation is comprised of a multitude of interdependent effects, the amount of cavitation activity in the cleaning liquid strongly depends on the sonication conditions. Cavitation activity as measured by ultraharmonic cavitation noise can be significantly enhanced when pulsed sonication is applied to a gas-supersaturated liquid under traveling wave conditions.
This enhancement results in a dramatic increase in particle removal, making it highly effective for megasonic cleaning applications such as those employing Space Alternated Phase Shift (SAPS™) technology from ACM Research. The optimal pulse parameters are determined by the dissolution time of the active bubbles, whereas the amount of cavitation activity depends on the ratio between pulse-off and pulse-on time, as well as the applied acoustic power.
Using SAPS for MLO
ACM successfully addresses MLO process complexities through our unique SAPS single-wafer manufacturing technology, delivering high throughput and superior removal performance. Our approach uses:
- A dual-filter system that ensures optimal cleanliness during manufacturing.
- Smart Megasonix™ systems that provide the precise combination of wet deposition and removal processes needed to lift the metal off the photoresist, leaving just enough to pattern the wafer
- Incorporation of the ProSys MegPie™ transducer and active puddle method
This combination enables fast, efficient removal with good uniformity and particle neutrality. These cleaning processes employ higher substrate rotation and approximately 1 liter per minute (l/pm) dilute fluid flows to achieve these goals. In fact, the ProSys MegPie transducer has become a standard in high-end megasonic enhanced particle removal, achieving greater than 98% particle removal efficiency (PRE) when measured at 19nm.
Why use an active puddle method for MLO and PR?
The active puddle method leverages the patented radial uniformity of the MegPie to enhance the chemical reaction kinetics by applying megasonic energy. Megasonic energy boosts the reaction kinetics by rapidly refreshing the chemistry at the surface and reducing the boundary layer depth. With megasonic energy, more benign chemistries at lower temperatures can be used to successfully complete these processes with cycle times measured in minutes.
Better Process Times & Lower Chemical Demand
The radial uniformity of the MegPie design assures that every portion of the substrate receives the same acoustic dosage, eliminating over-processing. Additionally, with the active puddle method, the substrate rotation is radically reduced. This enables the absolute minimum quantity of process chemistry to completely fill the gap between a MegPie resonator and substrate for proper operation.
By leveraging multiple, proven technologies, our approach to the MLO process significantly reduces process times and sharply reduces chemical demand and the need for high temperatures. This drives cost savings, better total cost of ownership and improves sustainability in semiconductor manufacturing. Contact us to learn more about how we can enhance your MLO processes.
Before and After illustration
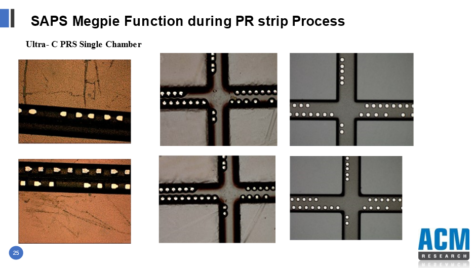